9e. Pleat & Stretch Soap Wrappers
Soap Manufacturing > 9. Soap Packaging
SOAP PLEAT WRAPPERS
Many
fancy fragrance soaps, gift soaps and upscale hotel soaps ore pleat wrapped.
This distinctive, luxury packaging style of unmistakable individuality is
applicable for round and oval shaped products with a side band. The soap pleat
wrappers are designed to wrap with twenty four pleats and to label soaps.
The typical capacities of automatic soap pleat
wrappers, according with the models, is in a range from 15 to 150 pleated soap
bars per minute.
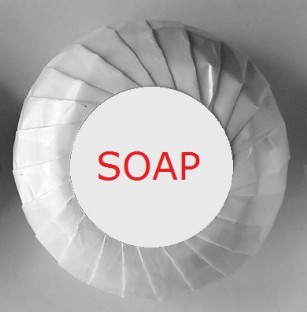
Also some models of manual pleat wrappers are used for small production
rate.
The wrapping material can vary from paper to transparent plastic film. Stamped soap are automatically fed onto an infeed conveyor. A vacuum suction cup transfers the soap from the infeed conveyor onto the reel fed wrapping material which was cut into an octagonal shape. The product together with its wrapping material is lowered into a pleating head assembly group. The folded pleats are securely maintained by a mechanically controlled iris system as the pleating head with the product inside moves to the labeling station, where the label is applied.
The wrapping material can vary from paper to transparent plastic film. Stamped soap are automatically fed onto an infeed conveyor. A vacuum suction cup transfers the soap from the infeed conveyor onto the reel fed wrapping material which was cut into an octagonal shape. The product together with its wrapping material is lowered into a pleating head assembly group. The folded pleats are securely maintained by a mechanically controlled iris system as the pleating head with the product inside moves to the labeling station, where the label is applied.
SOAP STRETCH WRAPPERS
Many Cosmetic, skin care and other types of specialty soaps are often stretch film wrapped and labeled. The use of this distinct, luxury packaging style is increasing worldwide. The soap stretch wrappers are designed to wrap with polyethylene stretch film and to label bar soaps and other solid products of all shapes.
The typical capacities of automatic soap stretch wrappers, according with the models, is in a range from 15 to 75 pleated soap bars per minute. Also some models of manual pleat wrappers are used for small production rate.
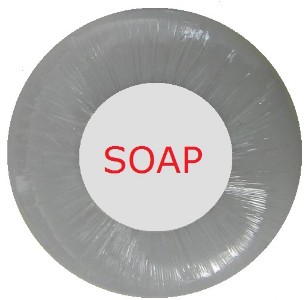
Usually the stamped soaps are hand fed one by one into a rubber pockets of the rotary indexing infeed table.
A vacuum suction cup moves the soap info the wrapping head assembly. The film is pre-stretched as the soap together with the film is lowered into the wrapping head assembly. An iris type closing mechanism stretches the film very tightly around the product. A hot knife cuts off the excess film and seals it. Two mechanical fingers remove and discard the film through a discharge tube into an excess film collecting container. A self-adhesive label is placed on top of each soap.