8e. Soap Plodders and Extruders
Soap Manufacturing > 8. Soap Finishing Line
SOAP PLODDERS
SIMPLEX REFINER PLODDER
Also the simplex refiner plodder is used in soap manufacturing to refine the soap: a combination of intimate homogenization and filtering of the soap. Simplex refiner plodder is a soap extruder composed by a screw made in aluminum alloy or in stainless steel, a barrel that is jacketed for cooling by means of a water chiller to avoid a production rate reduction, a hopper to feed the soap coming from the mixer, a strong gearbox and a basement. At the end of a refining plodder a drilled plate with rotary blades is assembled to extrude refined soap noodles.
DUPLEX VACUUM PLODDER
A duplex vacuum plodder is composed by 2 single simplex plodders connected by means of a vacuum chamber. The first plodder is called refining stage thanks to the drilled plate with blade, while the second plodder is called extrusion stage, for the presence of an extrusion cone assembled at the end of the machine. The two stages are connected with a chamber that work under vacuum to remove small bubbles of air that could be find in the extruded soap bar.
In the past the screws speeds was fixed but in the last 20 years, thanks to the frequency inverters, all the screws have an adjustable speed in r.p.m.
In the past the screws speeds was fixed but in the last 20 years, thanks to the frequency inverters, all the screws have an adjustable speed in r.p.m.
The extrusion cone is heated by means of an electrical heater to give a smooth surface to the extruded soap bar.
SPECIAL PLODDER
During the last 15 years, one of the most important Italian soap machines manufacturer developed a special duplex vacuum plodder able to refine and homogenize the soap, without the use of simplex refiner plodder and roll mill. This special soap plodder, called Transavon / Flexi plodder assembles one or two "combo-screws" (simplex or duplex) characterized by two different diameters that optimized the two main functions of a plodder screw: 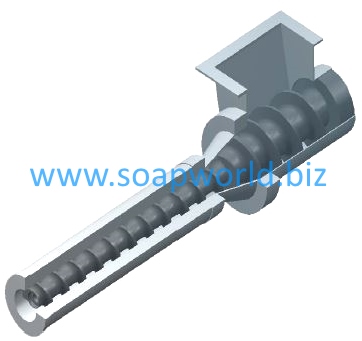
- The large diameter infeed section assures an optimal soap infeed.
- Small diameter and long compressing section assures maximum homogenization and compression.
The "combo- screw" has a long useful length with many spirals; the useful length of a combo-screw is 8-10 times the screws diameter. The high number of the spirals increases the working pressure of the soap. A Traditional plodder works the soap with a pressure up to 40 bars, while a "combo-screw" plodder is able to work the soap with a maximum pressure up to 100 bars. This high pressure allows the use of two refining screens in the last section of the barrel. A duplex "combo-screw" plodder assemble 2 refining screen on the first stage and 2 refining screen on the extrusion stage, before the extrusion cone.
8. Soap Finishing Line
8b. Soap Refining
8c. Mixers
8d. Soap Roll Mills
8e. Plodders
8f. Soap Cutters
8g. Soap Presses
8h. Chillers
8i. Accessories
8c. Mixers
8d. Soap Roll Mills
8e. Plodders
8f. Soap Cutters
8g. Soap Presses
8h. Chillers
8i. Accessories
>> INDEX
SOAP PLODDERS TECHNICAL DETAILS
Until now only single screw plodders are described, but the plodders can also be "twin screws", with 2 tangential and parallel screws to increase the production rate and to give a better homogenization to the soap.
The most important parameters for the plodder refining are three:
- The useful length of the screw. A long screw with many spirals works the soap at high pressure, increasing the homogenization. In the past the useful length of the screw was 3 times the diameter. Today the useful length of the screw is 4 times the diameter (for soap machines made in Italy). Special plodder can have a useful length of the screw up to 10 times the diameter. This parameter is called L/D ratio, where L is the useful length of the screw and D is the Diameter of the screw. For example a screw with an useful length of 1000 mm and a diameter of 250 mm has an L/D ratio of (1000/250 =) 4:1
- Refining screen. It is a grid assembled before the drilled plate. The screens are classified according to the number of wires per inch: 20 mesh screen means a grid with 20 metallic wires for each inch. The more powerful refining screen used in soap manufacturer is a 50 mesh screen, but also 20 and 30 mesh are used to grant a bigger production rate and to avoid soap heating due to a too dense refining screen.
- The shape of the screw. There are different types of the screws: with constant kernel diameter, with increasing kernel diameter, with constant pitch (distance from the spiral) and with variable pitch. The combinations of the 4 factors give screws with different features, like different soap compression and production rate.